Innovation drives competitiveness in functional textile yarns. High-Density Polyethylene (HDPE) yarn emerges as a high-performance material capturing industry attention. Its unique physical and chemical properties unlock tremendous potential in functional apparel, offering yarn manufacturers strategic opportunities for product diversification and market leadership.
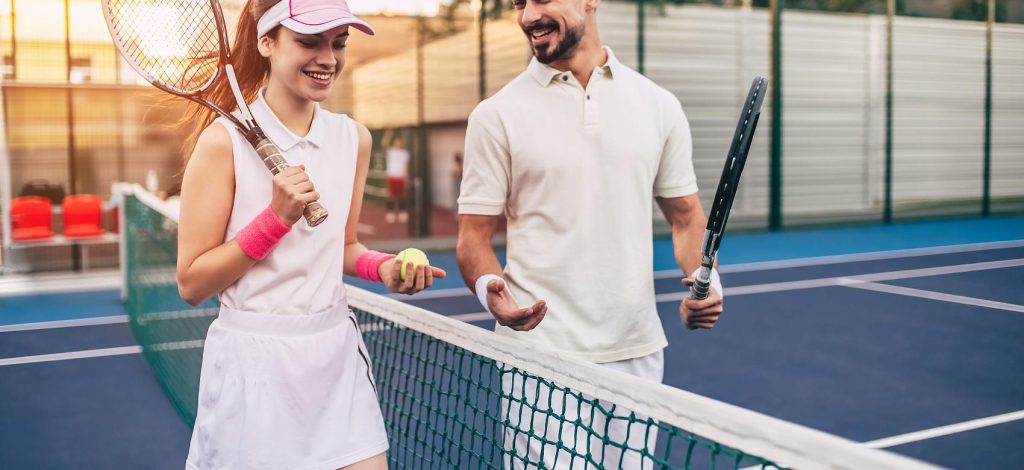
HDPE Yarn: Core Performance Analysis
High-Density Polyethylene (HDPE) is a cost-effective thermoplastic polymer renowned for its linear structure, high crystallinity, and unique mechanical-chemical property combination. With compact molecular chains and high crystallinity (>90%), HDPE delivers exceptional strength and rigidity across industries, including textiles.
HDPE achieves a unique balance between stiffness, strength, and flexibility—crucial for apparel applications. Despite high strength and rigidity, HDPE maintains lower stiffness than polypropylene while retaining flexibility. This combination enables strong durability with comfort and mobility, ideal for garments that are both protective and comfortable, extending applications from industrial textiles to wearable functional clothing.
Table 1: HDPE Yarn Key Performance Characteristics
Parameter | Value | Performance Advantage |
---|---|---|
Density | 0.94-0.97 g/cm³ | Lightweight construction, 30% lighter than cotton |
Thermal Conductivity | 0.5 W/(m·K) | Superior cooling effect, 5x faster heat dissipation |
Friction Coefficient | 0.1-0.2 | Ultra-smooth surface, silk-like feel |
From Pellets to Performance: HDPE Yarn Manufacturing
HDPE yarn production involves precision engineering with multiple critical steps ensuring final product performance and toughness: blending, extrusion, cooling, cutting, stretching, baking, and draw winding.
The process begins with uniform raw material mixing, followed by feeding HDPE pellets into screw extruders where they’re heated, melted, and extruded into films. Cooling and setting solidify the molten polymer. For high denier HDPE filaments, films are stretched and cut into specific width and thickness monofilaments. Stretching and setting enhance yarn strength and toughness, with optional baking for fiber optimization and continuous production through draw winding.
Unleashing Potential: HDPE Yarn Applications
HDPE yarn demonstrates tremendous functional apparel potential through its unique property combination: superior cooling performance, lightweight nature, wear resistance, and water repellency.
Key Applications:
Cooling Apparel & Bedding: HDPE yarn’s exceptional cooling performance positions it among the most effective cooling materials. Applications include cooling bedding and various clothing types, particularly valuable in warm climates or high-intensity activities, offering unique selling points for performance apparel and comfort textile markets.
Daily Commuter & Office Wear: HDPE yarn’s unique cooling properties make it ideal for professional attire worn in air-conditioned environments. Office workers wearing HDPE-based clothing experience enhanced cooling effects under air conditioning, allowing higher thermostat settings while maintaining personal comfort. This dual benefit reduces energy consumption and carbon footprint, making it an environmentally conscious choice for corporate wardrobes. Business shirts, blouses, and professional wear incorporating HDPE technology deliver both cooling comfort and sustainability benefits for the modern workplace.
HDPE yarn’s multiple functional characteristics—superior cooling performance, and lightweight nature—create a versatile fiber meeting multiple performance requirements simultaneously. One material provides comfort (lightweight, cooling), and durability (strength), reducing the need for fiber blending and simplifying design while potentially lowering manufacturing costs.
Table 2: 🎯 HDPE Yarn Applications vs Traditional Fibers
Application Scenarios | HDPE Yarn | Cotton | Polyester | Nylon |
---|---|---|---|---|
🛏️Home Textiles (Mattress, Bedsheets) | Ideal – Cooling Effect | Suitable | Suitable | Limited |
👕Summer Sportswear | Ideal – Heat Dissipation | Limited – Retains Moisture | Suitable | Suitable |
👶Baby Clothing & Sleepwear | Ideal – Ultra-Soft | Suitable | Limited – Less Soft | Limited |
🧦Seamless Underwear & Socks | Ideal – Smooth Feel | Suitable | Suitable | Suitable |
👟Shoe Uppers | Suitable – Breathable | Limited – Poor Durability | Suitable | Ideal – Durability |
👔Men’s Shirts & Casual Wear | Suitable – Professional Look | Ideal – Classic | Suitable | Limited |
👖Denim & Heavy Fabrics | Limited – Blending Only | Ideal – Traditional | Suitable | Limited |
🏭Industrial Textiles | Suitable – Cable Wrapper | Limited | Suitable | Ideal – Strength |
🌞UV Protection Fabrics | Suitable – Full Dull Series | Limited | Suitable | Suitable |
💡 Key Advantages of HDPE:
• Thermal Management: 0.5W thermal conductivity for superior cooling
• Comfort: Ultra-soft, silk-like hand feel with low friction coefficient
• Durability: Chemical resistance and anti-mildew properties
• Sustainability: Available in recycled and biodegradable variants
• Customization: 80+ dope-dyed colors and various specifications (30D-1200D)
Addressing Challenges: Strategic Innovation
Despite numerous advantages, HDPE yarn faces challenges in widespread apparel applications, with continuous innovation addressing these issues:
Dyeability: HDPE’s low water absorption and high crystallinity complicate traditional dyeing. Advanced techniques like dope dyeing achieve vibrant colors with excellent fastness. Annie’s Smartex PECOOX® exemplifies successful dope dyeing production.
Recyclability: HDPE ranks among the most recyclable plastics, enabling reuse in various products, reducing waste, and promoting circular economy.
Competitive Advantage: HDPE vs. Traditional Synthetic Fibers
Understanding differences between HDPE yarn and traditional synthetic fibers (nylon, polyester) proves crucial for strategic positioning.
Table 3: Performance Comparison – HDPE vs. Nylon vs. Polyester
Performance Features | HDPE Yarn | Cotton | Polyester | Nylon |
---|---|---|---|---|
🌡️Thermal Conductivity | Excellent (0.5W) | Poor | Moderate | Moderate |
🪶Softness & Hand Feel | Ultra-Soft (Silk-like) | Good | Moderate | Good |
💧Moisture Management | Water & Oil Repellent | Absorbs Moisture | Quick-Dry | Quick-Dry |
🛡️Chemical Resistance | Acid & Alkali Resistant | Poor | Good | Moderate |
🦠Antimicrobial Properties | Natural Anti-mildew | Prone to Mildew | Moderate | Moderate |
♻️Environmental Impact | Recyclable + Bio Options | Biodegradable | Non-biodegradable | Non-biodegradable |
🎨Color Fastness | Dope-Dyed (80+ Colors) | Moderate | Good | Good |
🏃Stretch & Recovery | Slight Stretch Available | Poor | Moderate | Excellent |
HDPE demonstrates exceptional performance in thermal management and moisture repellency while showing limitations in mechanical strength compared to engineered fibers like nylon and polyester. HDPE functions as a specialized textile solution for applications where cooling efficiency and chemical resistance are prioritized over structural performance—particularly in climate-comfort textiles and protective industrial applications.
Conclusion: Strategic Imperatives for Manufacturers
HDPE polyethylene yarn brings exciting opportunities to functional textiles. Its excellent strength, lightweight nature, superior cut resistance, and unique cooling performance make it key for meeting modern consumer demands for high performance and comfort.
The textile market moves toward sustainable, technologically advanced, high-performance directions. HDPE’s high recyclability and decreasing production carbon footprint align with current market trends. Emerging applications in smart textiles and wearable technology indicate tremendous growth potential in high-value, technology-integrated apparel.
By strategically leveraging HDPE’s unique properties and addressing challenges, functional yarn manufacturers can expand product lines and occupy leading positions in the evolving market, weaving an innovative future for functional textiles.